F-Scale Overview | Barbell Durability
April 29, 2024
Made In | Brand | Diameter | Finish Type | Tensile | Category | Rank | F Rating | RWH | High Repetition - CrossFit Affiliate | OLY Gym | Garage Gym | Power lifting Gym |
---|---|---|---|---|---|---|---|---|---|---|---|---|
28.50 | Stainless | 200,000 | 28.5MM Power | 1 | 100.00 | Yes | 200.00 | 1,500.00 | 2,857.14 | 30,000.00 | ||
Non-Rogue | 28.50 | Black Zinc | 200,000 | 28.5MM Power | 2 | 7.21 | No | 14.42 | 108.17 | 206.03 | 2,163.35 | |
Non-Rogue | 28.50 | Bright Zinc | 190,000 | 28.5MM Power | 3 | 6.10 | No | 12.20 | 91.49 | 174.27 | 1,829.81 | |
Non-Rogue | 28.50 | Raw Steel | 190,000 | 28.5MM Power | 4 | 5.04 | No | 10.08 | 75.56 | 143.93 | 1,511.25 | |
Non-Rogue | 28.50 | Chrome | 190,000 | 28.5MM Power | 5 | 0.79 | No | 1.57 | 11.80 | 22.47 | 235.91 | |
28.50 | Stainless | 200,000 | 28/28.5MM MULTI | 1 | 100.00 | Yes | 200.00 | 1,500.00 | 2,857.14 | 30,000.00 | ||
28.50 | Cerakote | 190,000 | 28/28.5MM MULTI | 2 | 8.00 | Yes | 16.00 | 120.00 | 228.57 | 2,400.00 | ||
28.50 | Black Zinc | 190,000 | 28/28.5MM MULTI | 2 | 8.00 | Yes | 16.00 | 120.00 | 228.57 | 2,400.00 | ||
28.50 | ECoat | 190,000 | 28/28.5MM MULTI | 2 | 8.00 | Yes | 16.00 | 120.00 | 228.57 | 2,400.00 | ||
Non-Rogue | 28.50 | Bright Zinc | 190,000 | 28/28.5MM MULTI | 5 | 6.78 | No | 13.56 | 101.71 | 193.74 | 2,034.25 | |
Non-Rogue | 28.50 | Cerakote | 190,000 | 28/28.5MM MULTI | 6 | 4.55 | No | 9.10 | 68.26 | 130.02 | 1,365.18 | |
Non-Rogue | 28.00 | Cerakote | 190,000 | 28/28.5MM MULTI | 7 | 3.47 | No | 6.94 | 52.03 | 99.10 | 1,040.56 | |
Non-Rogue | 28.50 | Black Zinc | 190,000 | 28/28.5MM MULTI | 8 | 2.63 | No | 5.27 | 39.52 | 75.28 | 790.48 | |
Non-Rogue | 28.50 | Cerakote | 190,000 | 28/28.5MM MULTI | 9 | 2.38 | No | 4.75 | 35.64 | 67.88 | 712.70 | |
Non-Rogue | 28.50 | Black Zinc | 190,000 | 28/28.5MM MULTI | 10 | 1.86 | No | 3.72 | 27.88 | 53.10 | 557.58 | |
Non-Rogue | 28.00 | Cerakote | 190,000 | 28/28.5MM MULTI | 11 | 1.38 | No | 2.76 | 20.73 | 39.48 | 414.58 | |
Non-Rogue | 28.00 | Chrome | 190,000 | 28/28.5MM MULTI | 12 | 0.96 | No | 1.92 | 14.41 | 27.44 | 288.12 | |
Non-Rogue | 28.00 | Black Zinc | 205,000 | 28/28.5MM MULTI | 13 | 0.94 | No | 1.88 | 14.13 | 26.91 | 282.57 | |
Non-Rogue | 28.50 | Chrome | 190,000 | 28/28.5MM MULTI | 14 | 0.91 | No | 1.83 | 13.70 | 26.09 | 273.92 | |
28.00 | Stainless | 200,000 | 28MM OLY | 1 | 100.00 | Yes | 200.00 | 1,500.00 | 2,857.14 | 30,000.00 | ||
28.00 | Cerakote | 215,000 | 28MM OLY | 2 | 6.00 | Yes | 12.00 | 90.00 | 171.43 | 1,800.00 | ||
Non-Rogue | 28.00 | Chrome | 215,000 | 28MM OLY | 3 | 1.59 | No | 3.19 | 23.92 | 45.56 | 478.35 | |
Non-Rogue | 28.00 | Chrome | 190,000 | 28MM OLY | 4 | 1.15 | No | 2.29 | 17.21 | 32.78 | 344.20 | |
Non-Rogue | 28.00 | Chrome | 190,000 | 28MM OLY | 5 | 1.07 | No | 2.14 | 16.03 | 30.54 | 320.63 | |
Non-Rogue | 28.00 | Chrome | 200,000 | 28MM OLY | 6 | 0.75 | No | 1.50 | 11.22 | 21.38 | 224.47 | |
29.00 | Stainless | 200,000 | 29MM Power | 1 | 100.00 | Yes | 200.00 | 1,500.00 | 2,857.14 | 30,000.00 | ||
29.00 | Black Zinc | 205,000 | 29MM Power | 2 | 8.00 | Yes | 16.00 | 120.00 | 228.57 | 2,400.00 | ||
29.00 | Raw Steel | 205,000 | 29MM Power | 2 | 8.00 | Yes | 16.00 | 120.00 | 228.57 | 2,400.00 | ||
29.00 | Cerakote | 205,000 | 29MM Power | 2 | 8.00 | Yes | 16.00 | 120.00 | 228.57 | 2,400.00 | ||
Non-Rogue | 29.00 | Raw Steel | 215,000 | 29MM Power | 5 | 3.82 | No | 7.63 | 57.23 | 109.02 | 1,144.68 | |
Non-Rogue | 29.00 | Stainless | 200,000 | 29MM Power | 6 | 2.84 | No | 5.67 | 42.54 | 81.02 | 850.72 | |
Non-Rogue | 29.00 | Chrome | 190,000 | 29MM Power | 7 | 2.14 | No | 4.28 | 32.07 | 61.09 | 641.42 | |
Non-Rogue | 29.00 | Chrome | 216,200 | 29MM Power | 8 | 1.75 | No | 3.50 | 26.24 | 49.98 | 524.74 | |
Non-Rogue | 29.00 | Raw Steel | 210,000 | 29MM Power | 9 | 1.10 | No | 2.20 | 16.51 | 31.44 | 330.15 | |
Non-Rogue | 29.00 | Chrome | 200,000 | 29MM Power | 10 | 0.99 | No | 1.99 | 14.91 | 28.40 | 298.25 | |
Non-Rogue | 29.00 | Bright Zinc | 250,000 | 29MM Power | 11 | 0.67 | No | 1.35 | 10.11 | 19.25 | 202.17 |
- We were unable to get the stainless RWH samples to fail in our test.
- All barbells were acquired and tested in 2024
ROGUE MANUFACTURES THE WORLD’S MOST DURABLE BARBELLS
This is How We Did It
Rogue spent a decade and over $2,000,000 in scientific testing, research, and development to make our bars more durable than any other bars on the market. We have optimized our materials and manufacturing processes. We also developed a proprietary, patented process we call Rogue Work Hardening™ (RWH). Barbells treated with RWH™ are more resistant to the stresses of being repeatedly dropped. Rogue launched this project because of an unprecedented change in the manner in which barbells are used. The widespread introduction of high repetition Olympic Weightlifting movements resulted in extraordinary increases in the demands placed on bars. Rogue has also developed a clear and meaningful scale for rating barbell durability that makes it easy for you to choose the correct barbell for your application.
Read more about the science of RWH™ and the F Scale™ here.
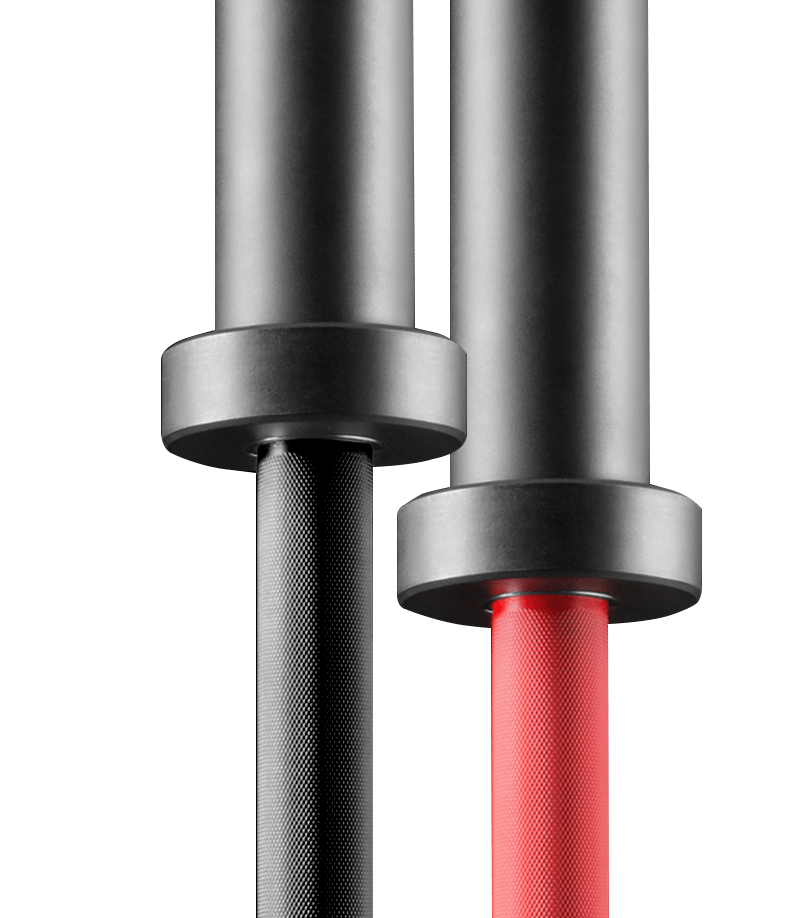
Durability Improvements
Rogue’s team of engineers and materials scientists studied the use and abuse that cause the most stress to barbells. They studied alloys and manufacturing processes from across many different industries and developed a plan to make our bars as durable as possible.
The Right Steel
The first step was to optimize our steel alloys’ chemical and mechanical properties. Barbells with low tensile and yield strength are more likely to bend with normal use. Tensile and yield strength that is too high can be detrimental, making the metal brittle.
The Right Plating
The second step was to rethink barbell coatings. Chrome has been the “gold” standard of barbell plating for many, many years. Rogue’s exhaustive scientific analysis has shown conclusively that chrome decreases the durable lifespan of barbell shafts. Chrome remains an excellent, wear resistant sleeve coating and Rogue will continue to use it for this application.
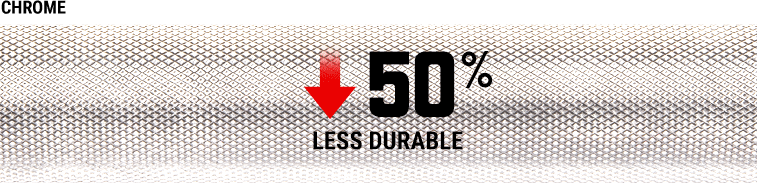
Rogue Work Hardening™
The final step was to find a way to make our barbells resistant to the stresses of being dropped. To this end, Rogue developed the proprietary, patent pending process Rogue Work Hardening (RWH™). Thousands of hours of independent scientific fatigue testing and analysis demonstrate conclusively that Rogue barbell shafts treated with RWH™ have improved durability and last longer than untreated bars when subjected to the stresses of being dropped.
Read more about Rogue Barbell durability improvements here.
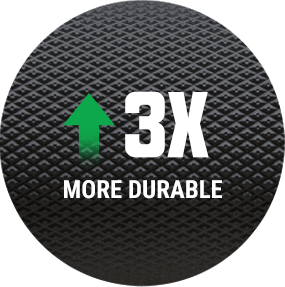
Change In Use
Dropping the bar during Olympic weightlifting produces far more stress on a barbell shaft than traditional bodybuilding movements and powerlifting movements. It follows then that historically, the bars subjected to the greatest stresses were in Olympic Weightlifting training centers. Bars at large facilities were dropped 10,000-20,000 thousand times per year.
Around 2005, high repetition Olympic Weightlifting movements gained popularity and bumper plates became more readily available. From that point on it became common for bars to be dropped up to 150,000 times per year in gyms. This is up to a 15x increase in drops.
Read more about the history and evolution of barbell use here.
Determination of Stresses Placed On A Barbell
Because of the extraordinary change in barbell usage, we decided to consult with the failure analysis engineers at SEA Limited, a world leader in consumer product testing, to learn about the stresses that are placed on a barbell when dropped.
To determine these stresses, electronic strain gauges were attached to the shaft of a barbell and the bars were dropped from overhead.
Read more about the determination of the stresses placed on a barbell here.
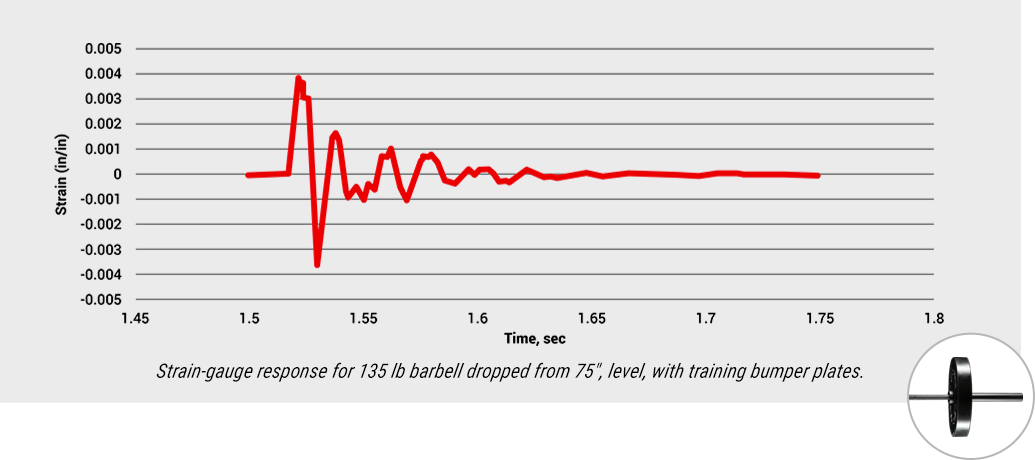
What Causes The Most Stress
SEA found that the greatest stress on a barbell shaft is caused not by heavy weight loads, but by the unsupported / unloaded end of the sleeve continuing its downward momentum after the plates have hit the ground from an overhead drop. As seen in the illustrations below, the stress will continue to increase as the unsupported length of sleeve increases
Naturally then, when the barbell sleeve is shorter in overall length (such as those on a C-70S Short Bar) the force of the unsupported end of the sleeve is less. A similar situation is found when a standard length sleeve is supported by additional plates and is able to remain more level when the plates hit the ground. Both of these situations greatly reduce the stress on the shaft when the bar is dropped.
1. High Stress
2. Medium Stress
3. Low Stress
Understanding that weight loads don’t dictate stress can affect how we look at typical barbell usage. For example, in a gym that practices mainly high-repetition, low weight Olympic Weightlifting movements (65-135 LBS), the highest number of cycles are actually placed on barbells at their highest levels of stress, with long lengths of unsupported sleeves. To put it in another perspective, the drop of a standard men’s bar with relatively light weight (shown in the video on the right) causes much more measurable stress than the lift and drop of an Elephant Bar™ loaded to over 1,000 LBS.
Unsurprisingly, lifts that are not dropped—even extremely heavy ones—also cause far less stress than lifts that are dropped.
Read more about what causes stress to a barbell here.
Laboratory Simulation of the Stress of Dropping A Bar
Once Rogue determined the stresses that are placed on barbells, the engineering team used a 4 point bend test to simulate this stress in a testing environment. The sample is fixed at the ends and the load is delivered by two pins, two inches apart. This load is cycled several times per second.
Read more about the determination of the stresses placed on a barbell here.
The F Scale™
Choosing the right barbell can be difficult. There is no industry standard for reporting barbell properties. Therefore, you are presented with an array of numbers which vary by manufacturer and very often do not provide useful information. Rogue has developed a clear and meaningful scale for rating barbell durability that makes it easy for you to choose the correct barbell for your application.
By testing finished barbell shafts using the 4-Point Bend Test at a stress level appropriate for the bar’s sleeve type, we are able to assign a durability rating or F Rating™ to each barbell. Performing the test in this manner accounts for all of the factors that contribute to barbell durability when subjected to the forces of being dropped from overhead. More specifically, the F Rating of a barbell is directly correlated to the number of cycles the shaft lasts in the 4-Point Bend Test, when tested at a stress level appropriate for the type of sleeve used on the bar.
As an example, if we have a 28MM chrome plated bar with a tensile strength of 215,000 PSI, and it lasts 35,000 cycles when tested at the stress level for a standard men’s sleeve, that bar would receive a rating of F1. A shaft tested in the same manner that lasts twice as long (70,000 cycles) receives a rating of F2, and a shaft that lasts 3x longer than that (210,000 cycles) would receive a rating of F6. Bars with shorter sleeves will perform better in this test, as will those that are media blasted. The effects of our Rogue Work Hardening™ process, importantly, extend much deeper than media blasting, and have been shown to retain their benefits even when confronted with scratches. Bars treated with RWH™ are designated by having an R in their F Rating™. When combined with a shorter sleeve design, these RWH™ bars produce the highest marks on the F Scale, with the pinnacle set at F-16R.
Read more about the F Scale™ here.
Application
How a barbell is used will affect its durable lifespan, and it’s a key factor in determining what type of F Rating™ might be suitable for your gym’s needs.
As we’ve established, dropping a bar from overhead causes more stress on the shaft than traditional bodybuilding or powerlifting movements. A barbell used primarily for slow lifts will typically last much longer than the same barbell used for Olympic Weightlifting. Bars used in commercial facilities will also see more volume and therefore more cumulative stress than barbells used by single athletes.
This graph correlates the F Rating™ of a barbell with different types of usage in order to predict the durable lifespan. Using this data, we are able to make recommendations on what F Rating™ is appropriate for different training situations.
Conclusion
Rogue has created an industry standard for the durability rating of barbells. The big winner with this scale is the customer. Rather than relying on a meaningless static strength rating or trying to make sense of tensile and yield strength, you can know how durable your bar is compared to other bars on the market.
Our hope is that the F Scale will expand beyond Rogue and allow customers use F Ratings when choosing the bar for their application regardless of the manufacturer.
Rogue openly invites any brand to bring your engineers and barbell steel with plating variants to Columbus, Ohio. We will open up the lab and let you test your bars. We only ask that you are honest with your customers when you see the results. Once we test your steel, we will add it to the data we have collected to better refine the F Rating.
We have tested most of the barbell competitors from around the globe. Simple things we know from this testing annually thru February of 2024:
- Chrome is not good for barbell durability
- 28MM for high repetition gyms such as CrossFit affiliates is a poor design choice. Coupling this with chrome is even worse. Painting the bar orange does not impact strength or durability!
- US Sourced steel barbell manufacturers are more durable as of February 2024. Barbells tested from China consistently test low on durability
- Rogue Stainless Barbells with RWH are the most durable barbells on the planet
Read more about the research and development that went into creating the F Scale™ here.
Rogue, F Scale, and related registered and non-registered logos and marks are registered and non-registered trademarks of Rogue Fitness and may not used without the express prior written consent of Rogue Fitness. This includes without limitation the data generated and output by the calculator, which may not be used for advertising or marketing purposes by anyone other than Rogue. If you are a manufacturer of retailer of non-Rogue products who is interested in using the F Scale you may contact us at bartesting@roguefitness.com.